The national electric grid forms the bedrock of the American economy, but it suffers from dangerous vulnerabilities. One of them is a shortage of transformers — the voltage-converters critical to electrical transmission and distribution. These shortfalls hamper our national energy policy and the path to building a sustainable grid. Ensuring a robust reserve of transformers is a simple first step to support grid resilience and allow for the buildout of electric infrastructure that would enable cleaner and greener power. In the process, such a stockpile would bolster domestic manufacturing, spur job creation, and strengthen national security.
Electric transformers are a critical piece of the national electrical grid. Power stations generate electricity at high voltage, which has more stringent safety requirements than the electricity used every day by households and businesses. Transformers are the equipment that changes, or “steps down,” the voltage level so it can be safely distributed to communities. They range in size from small transformers perched atop electric poles to the 600,000-pound large power transformers (LPTs) found at the 55,000 regional substations in the U.S. Over 90 percent of the electricity consumed in the U.S. passes through LPTs, making them the backbone of the nation’s high-voltage bulk-power system. High Voltage Power Transformer
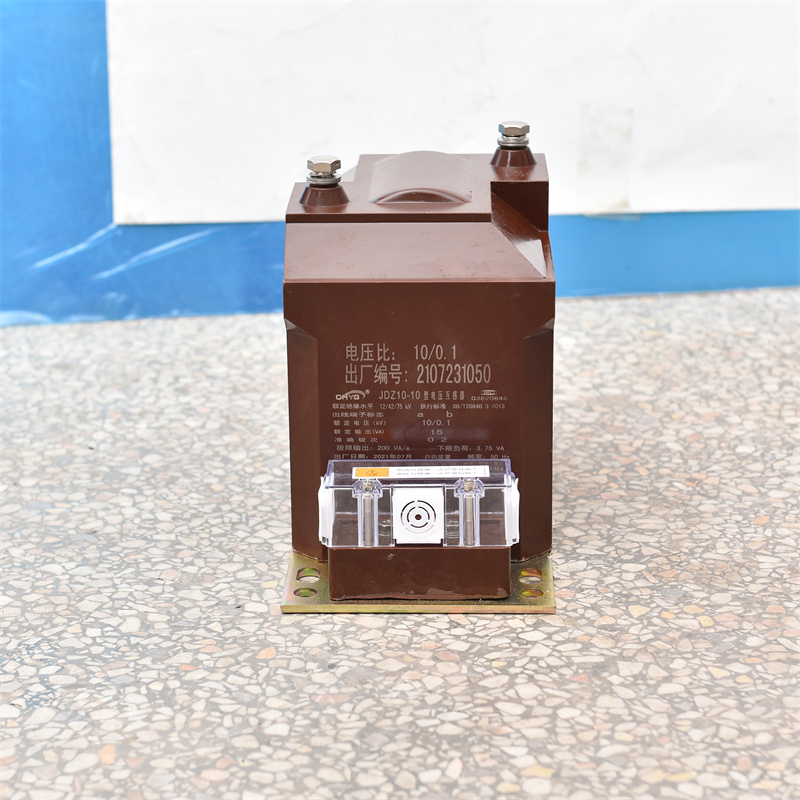
LPT failure or disruption has an outsize impact. Outages leave customers in the dark and constrain the functioning of commerce, schooling, and many other elements of modern American life. Common disruptors include major weather events like hurricanes, floods, and tornadoes. But that’s not the only threat: The nation has registered at least eight attacks on power substations in four states in recent weeks. The latest occurred on Christmas Day, when four substations in Washington state were attacked. Previous attacks on substations in North Carolina disabled two transformers, with the result that 45,000 customers lost heat and running water for up to three days in the middle of winter. In 2013, a sniper shot and severely damaged 17 LPTs during an isolated assault on a California substation. These high-risk emergencies underline the grid’s vulnerability to sudden and unexpected transformer losses.
The Federal Energy Regulatory Commission and the North American Electric Reliability Corporation have both warned that transformer failures could inflict a large cost on the nation’s economy, public health, and security interests.
Ongoing supply chain shortages make it difficult to maintain the electric grid and exacerbate the impact of transformer disruptions. Approximately 80 percent of transformers are manufactured abroad. Transformer components such as digital monitoring devices and remote sensors are vulnerable to hacking, leading to a 2020 executive order that authorized federal officials to ban the domestic use of electronic components produced by companies with connections to “foreign adversaries.”
Additionally, current transformer supplies are inadequate to meet the projected demands of green energy infrastructure. The Biden administration has committed to halving U.S. carbon emissions by 2030 and zeroing them out by 2050. Studies from Princeton, MIT, and National Renewable Energy Laboratory show that to achieve such rapid rates of decarbonization, transmission infrastructure will have to double or triple over the next 30 years. Otherwise, renewables will not be able to connect to the grid or send the electricity they produce to end users. Long delivery times, high prices, and reliance on international transformer manufacturers will limit our ability to realize construction at such an unprecedented pace.
The average cost of transformers has doubled or tripled since 2020, and the lag between order and delivery has grown from three months to a year. A 2020 report from the Department of Commerce found that the average transformer is 30 to 40 years old — far beyond the intended lifespan of 25 years. The age of our current stock suggests that active transformers may be more vulnerable to mechanical breakdowns and failure. This reflects a broader trend of underinvestment in maintenance and modernization of electric infrastructure.
The transformer manufacturing industry was decimated by offshoring. The remaining eight U.S.-based companies that produce transformers satisfy only about 20 percent of the market, leaving America’s 3,000 domestic electric utilities vulnerable to supply chain disruptions. This was starkly evident in the wake of the pandemic. The prior transformer deficit was exacerbated as lockdowns scrambled supply chains and energy loads fluctuated widely in response to the shift to remote work. Major storms, fires and hurricanes in the past two years have also led to substantial reductions in inventory. Since 2020, prices for some specific transformers have increased as much as 900 percent. Foreign producers have also been suspected of trying to corner the large transformer market by bidding low to drive competitors out of business.
LPT manufacturing is a skill- and resource-intensive process, with a single unit costing $4 million or more. LPTs are typically custom-built, with exacting technical specifications and high safety standards. Specially trained engineers design LPTs and experienced technicians assemble the rare, highly sensitive components into the final product. Their size and delicate machinery make transportation, installation, and maintenance an expensive undertaking.
A shrinking labor pool is one of the main challenges to scaling up transformer manufacturing. The one-two punch of offshoring and a decrease in vocational training left manufacturers of transformers and their components with an aging workforce and few opportunities to attract new employees. The decline in vocational education has shrunk the pool of individuals who have the skills required for transformer manufacturing, such as welding, coil winding, and transformer testing. Welders are particularly sought-after, but unlike electricians or carpenters, they do not have a single union where employers could easily find them. Transformer manufacturing also requires electrical engineers. But the majority of electrical engineers pursue electronics or computer science employment, while few postsecondary institutions offer the required specializations in manufacturing, power, or electrical design engineering. Addressing the skills mismatch and training a younger workforce are longer-term endeavors that should start as soon as possible.
Policymakers must not only address the immediate need for transformers but also develop a longer-term base of production that can provide a robust and accessible supply.
In the near term, the Biden administration and Congress should consider the following actions:
Long-term solutions require addressing industry-wide challenges to scaling manufacturing, including securing resources and growing the labor pool. Workforce development can occur through the private sector, agencies, and legislative actions. The following policies should be considered:

Lightning Resistor Transformers are a fundamental component of our electric grid. Securing the transformer supply chain is critical to ensure the grid’s resilience, strengthen national security, and build a decarbonized future. Longstanding domestic manufacturing deficiencies exacerbated by the pandemic have left us with an urgent need for federal action. Policy solutions like those outlined above will create opportunities to boost domestic employment and guarantee a resilient electric grid.